![]() |
---|
OUR CHALLENGE
How might we
improve the logistics management workflow
and ensure content
identification on deck?
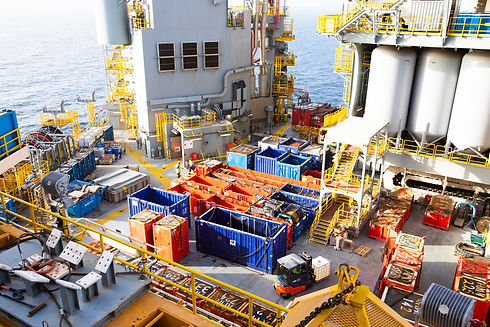
INVENTORY MANAGEMENT
As mentioned earlier, the remaining tabs facilitate the specific tasks that our three users must complete to keep operations running on the platform. Interactions with inventory in the system are done through our app, available to the service company for making requests of needed items during daily operations, and to deck workers through tablets attached to their forklifts. Once a request is made on the Requests tab, it appears as a task for completion on the deck worker’s tablet. With the real-time location of all the containers now available on the Inventory tab, life is easy for deck workers who need to locate and deliver requested items. The web application also keeps track of the status of each container and all the items in the inventory, a feature that saves operators huge amounts of rent paid on equipment that are long overdue for return. When these items are ready to be shipped back on shore, they are sent to the Backload tab and picked up on the next boat out.
OUR PRODUCT
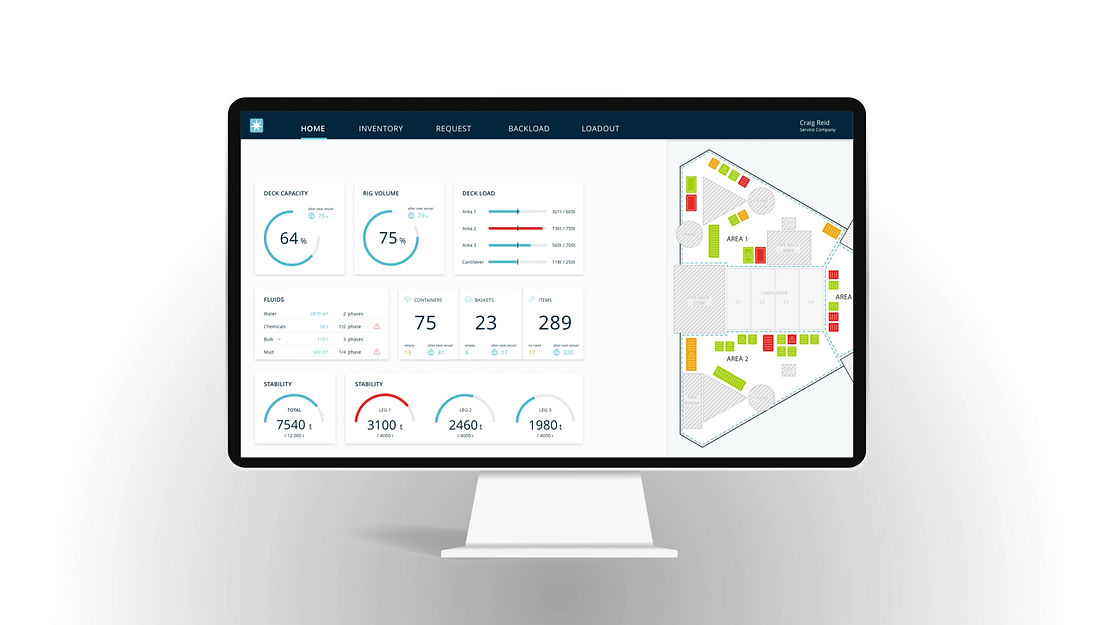
USER-FRIENDLY DASHBOARD
It is important for our three users to have a grand overview of all rig operations through the dashboard screen on the web application. Employees on their tablets or computers can quickly see when the next supply boat is arriving, how much container capacity exists on the platform, and what types of materials are currently on board. This screen is updated any time a new container arrives from the shore, and gives status updates on individual materials needed for the drilling operations. For handling more specific day-to-day tasks, deck workers and drilling engineers can navigate across the other tabs of the web application.

TRACKING OF ITEMS
Upon arrival of the supply vessel, the service company will sync the shipment's cargo list with the web application on the Loadout tab. The containers are then offloaded and a beacon box (with computer vision) is used to take a picture of the container ID for pairing. Once the status of linking is confirmed, the beacon box is attached to the container for real-time location visibility. This step links the container ID to a beacon. During the pairing step, the ID captured by the camera is confirmed on the active manifest within the web application. This step completes the receipt of cargo into our system and enables the ease of location of items on the rigs; eliminating about 7hrs a day directly/indirectly used in searching for items on deck.

USER-FRIENDLY DASHBOARD
It is important for our three users to have a grand overview of all rig operations through the dashboard screen on the web application. Employees on their tablets or computers can quickly see when the next supply boat is arriving, how much container capacity exists on the platform, and what types of materials are currently on board. This screen is updated any time a new container arrives from the shore, and gives status updates on individual materials needed for the drilling operations. For handling more specific day-to-day tasks, deck workers and drilling engineers can navigate across the other tabs of the web application.

USER FEEDBACK
Craig
Drilling Engineer
"Requesting for material has improved 100% for me! No request is lost, I don’t have to wait that long and I can plan ahead better.
Johanna
Operator
"Managing everything with Oceanlog saved us a lot of money. We finally have an overview of what is going on and can manage the operation at the best time for value."
Egon
Deckworker
"It is a great benefit to know where all items are located. My Workflow is faster, more structured, and less stressful now!"


